
The concept of crushing ratio is often used to measure the crushing effect of the crusher. The crushing ratio of the crusher is the ratio of the raw material particle size to the particle size of the crushed product. It indicates the multiple of the raw material reduction after crushing.
There are several ways to calculate the crushing ratio (i):
(1) Calculate by the ratio of the maximum particle size of the material before crushing to the maximum particle size of the product after crushing:
Where Dmax is the maximum particle size of the material before crushing;
dmax is the maximum particle size of the material after crushing.
Due to different customs in different countries, the method of determining the maximum particle size is also different. The UK and the US use the sieve hole width that allows 80% of the material to pass through the sieve hole as the diameter of the maximum particle size; my country and the former Soviet Union use the sieve hole width that allows 95% of the material to pass through the sieve hole as the diameter of the maximum particle size.
(2) Calculate by the ratio of the effective width of the crusher feed port and the width of the discharge port:
Where B is the width of the crusher feed port;
b is the width of the crusher discharge port.
The 0.85 in the formula is the effective width coefficient to ensure that the crusher bites the material. The value of the discharge opening width b is that the coarse crusher takes the maximum discharge opening width, and the medium and fine crushers take the minimum discharge opening width.
It is very convenient to calculate the crushing ratio using formula (1-2), because it is impossible to frequently perform screening analysis on a large number of materials in production, but as long as the width of the crusher feed opening and discharge opening is known, the crushing ratio can be calculated according to formula (1-2).
(3) Calculation using average particle size:
Where Dcp is the average diameter of the material before crushing;
dcp is the average diameter of the material after crushing.
The crushing ratio obtained by this method can more realistically reflect the degree of crushing. Therefore, it is used in theoretical research.
The double-rotor crusher produced by our company has effectively solved the problem of less fine powder in the crushing section of the brick factory, resulting in rough bricks and unstable quality. It truly achieves that after one crushing, 50-80 mesh accounts for 50%-60%. Professionally crushing coal gangue, shale, slag, and help the crushing work of the brick factory and improve efficiency.
Use coal gangue and shale to produce sintered bricks and tiles. These brick and tile enterprises use a variety of crushing equipment, including traditional hammer crushers, impact crushers, wear-resistant crushers, etc. However, due to the huge amount of return materials after crushing and screening, it is often difficult to crush them after several rounds. Therefore, after years of tracking, investigation, careful research, and precise design, our company has manufactured a double-rotor hammer crusher to fill the gap in the crushing problem.
Henan easyrock Heavy Industry Machinery Manufacturing Co., Ltd. has focused on crushers and grinders for 20 years. Various hammer crushers, two-stage crushers, and heavy crushers can be customized according to the specific conditions of the construction site, with preferential prices. easyrock Heavy Industry is dedicated to serving you.
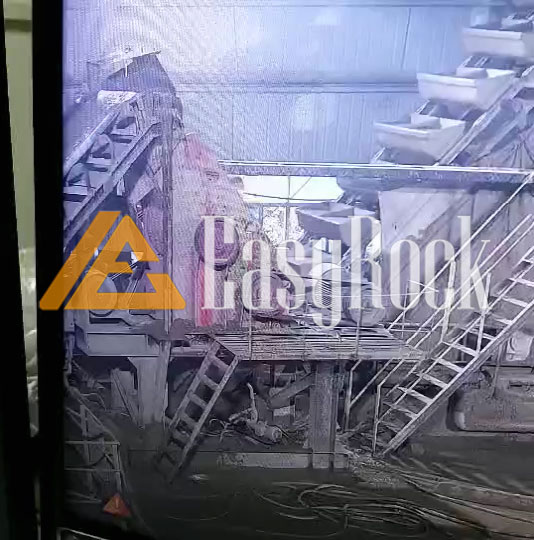